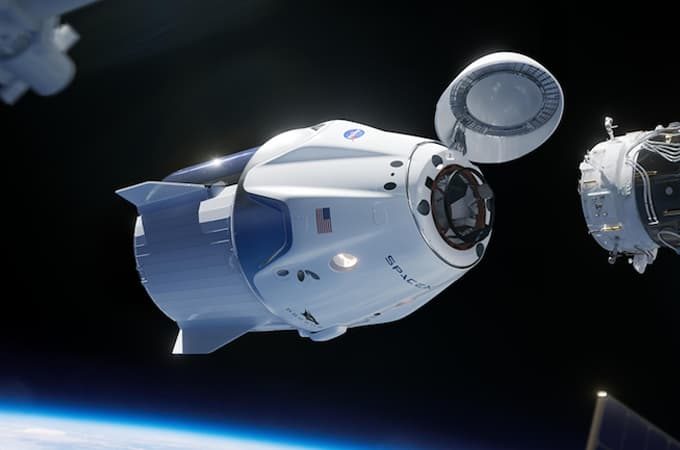
Materials used for laser cutting in the aerospace industry are Chin alloys, nickel alloys, chromium alloys, aluminum alloys, stainless steel, molybdenum citrate, plastics, and composite materials. In the manufacture of aerospace equipment, the shell is made of special metal materials with high strength, high hardness, and high-temperature resistance. It is difficult to complete the processing of materials by ordinary cutting methods. Laser cutting is an efficient processing method, which can be used to process aircraft skins, honeycomb structures, frames, wings, tail shields, helicopter main rotors, engine cases, and flame tubes. Laser cutting generally uses continuous output lasers, but also high repetition frequency carbon dioxide pulsed lasers. The aspect ratio of laser cutting is high. For non-metals, the aspect ratio can reach more than 100, and the metal can reach about 20.
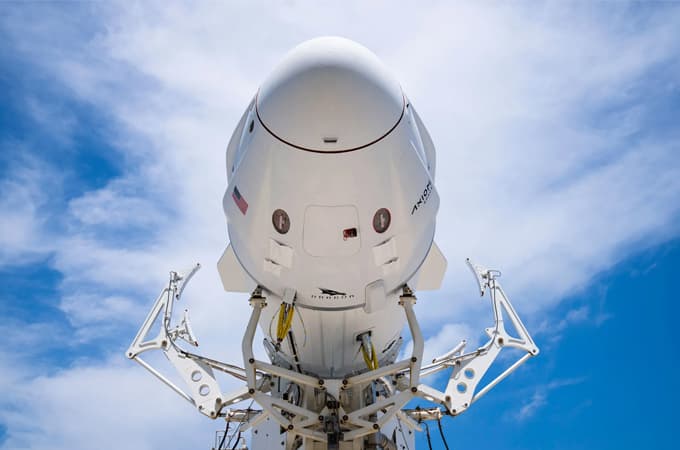
The laser cutting speed is high, the cutting of Qin alloy sheet is 30 times that of the mechanical method, and the cutting of the steel plate is 20 times that of the mechanical method. Compared with oxyacetylene and plasma cutting methods, the quality of laser cutting is better.
In the aerospace industry, many parts are welded with electron beams. Since laser welding does not need to be performed in a vacuum, electron beam welding is currently being replaced by laser welding. For a long time, the connection between aircraft structural parts has been using the backward riveting process. The main reason is that the aluminum alloy material used in the aircraft structure is heat treatment strengthened aluminum alloy (ie, high-strength aluminum alloy). Once welded, the heat treatment strengthening effect will be lost, and intergranular cracks are difficult to avoid. The use of laser welding technology overcomes such problems and greatly simplifies the manufacturing process of the aircraft fuselage, reducing the weight of the fuselage by 18% and the cost by 21.4% to 24.3%. Laser welding technology is a technological revolution in aircraft manufacturing.
Laser drilling technology is used in the aerospace industry for instrument gemstone bearings, air-cooled turbine blades, nozzles, and combustion chambers. At present, in terms of machining aero-engine parts, laser drilling is limited to machining cooling holes in stationary parts of the engine because of the presence of microscopic cracks on the surface of the holes. After a comprehensive analysis, laser drilling has the advantages of good effect, strong versatility, high efficiency, and low cost.
Laser cladding is an important material surface modification technology. In aviation, spare parts for aero-engines are expensive, so in many cases, it is cost-effective to repair parts. But the quality of the repaired parts must meet safety requirements. For example, when damage occurs on the surface of an aircraft propeller blade, it must be repaired by some surface treatment techniques. In addition to considering the high strength and fatigue resistance required for propeller blades, the corrosion resistance after surface repair must also be considered. Laser cladding technology can be well used for three-dimensional surface cladding repair of engine blades.
The application of laser forming manufacturing technology in the aviation field is directly reflected in the direct manufacturing of titanium alloy structural parts for aviation and the rapid repair of aero-engine parts. Laser forming manufacturing technology has become one of the core manufacturing new technologies for large-scale titanium alloy structural parts of aerospace defense weapons and equipment. Laser forming manufacturing technology has changed the disadvantages of traditional manufacturing methods, such as high cost, long preparation time for forging molds, the large amount of machining, and low material utilization.